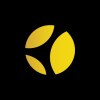
AB InBev Africa
About the job
Dreaming big is in our DNA. It’s who we are as a company. It’s our culture. It’s our heritage. And more than ever, it’s our future. A future where we’re always looking forward. Always serving up new ways to meet life’s moments. A future where we keep dreaming bigger. We look for people with passion, talent, and curiosity, and provide them with the teammates, resources and opportunities to unleash their full potential. The power we create together – when we combine your strengths with ours – is unstoppable. Are you ready to join a team that dreams as big as you do?
The key purpose of this role is the operation and cleaning of the germination out transfer systems, kilning, Malt Analyses Bins and monitor the effluent system. Through the execution of VPO routines which include but not limited to the execution of quality control checks, analyses and problem solving. Training, coaching and assessing (OWD) of other team members and supporting the maintenance department in execution of their routines.
Key roles and responsibilities:
Safety and environment
Lead and execute the territorial safety ownership and checks
Monitor safety and environment risks on shift
Implement mitigation measures to eliminate risks
Shift based production performance and processes
Interpret production plan for shift and ensure kilns are ready on time for the pieces
Monitor kilning processes on shift
Monitor effluent systems
Ensure process quality analyses are done and recorded on shift
Ensure and maintain a safe and healthy work environment
Co-ordinate autonomous operations and cleaning
Ensure transfer systems and vessels are cleaned to standard through hygiene audits
Ensure 5S and ATO execution
Shift team performance
Communicate effectively in the workplace with all key stakeholders (i.e. MTO, Boiler House, Silo Block)
Engage in handover meetings through updated OWS (handover books and SIC boards)
Ensure effective transfer of information between shifts
Follow escalation processes
Perform administration
Ensure application of VPO and associated digital tools
Contribute to self and team development
Ensures all checks and analyses are recorded in respective charts / sheets / SIC / digital tools and Boards
Review SOPs according to review plan and or OWD plans
Problem solving
Apply problem solving and decision-making techniques and principles
Problem solving terminator or any other problem-solving tool relay to be followed
Ensure root cause analyses is completed for all deviations according to problem solving trigger list, including process and breakdown triggers
Key attributes and competencies:
Communication
Actively participate in shift meetings, asking questions to test understanding and contributing suggestions. making use of the action log to record issues, problems and improvement opportunities
Fully understand the team goals and participate in team goal review sessions
Make use of relevant communication media (e.g. operator workstations/team rooms) to stay informed and inform others of issues
Complete required hand over to incoming shift team members, ensuring the issues relating to plant performance, quality and maintenance are communicated
Problem-solving
Where problems occur (or triggers are met), use quick fix routines and Problem Terminator 5Y’s to identify the possible root cause and escalate to Process Lead where support is needed
All breakdowns must be logged on SAP and the root cause element be done on problem terminator
Continuous improvements
Identify sources of waste and report these to the Process Lead
Drive KPI’s to achieve Plant Excellence
Raise innovations on the correct platforms
Recognise peers on the associated platforms and participation in routines such as Results Sharing
Minimum requirements:
Matric or equivalent e.g. NQF level 4
Min – 6 months on the job training
Desirable but not essential:
Post Matric qualification
National Diploma or equivalent in Engineering/Sciences
General Certificate in maltings (GCM)
12 months on the job training
100% SKAP in at least one other role
1 – 3 years experience in a malting environment
Previous experience in a process-controlled manufacturing environment, ideally in food FMCG products.
Additional information:
Band: XI
SAB/ABInBev is an equal opportunity employer and all appointments will be made in line with SAB/ABInBev employment equity plan and talent requirements. The advert has minimum requirements listed. Management reserves the right to use additional/ relevant information as criteria for short-listing.
In accordance with South African Breweries Pty (ltd) duty to provide and maintain a workplace that is safe for of our employees and their families, our customers and visitors, and the community at large from infectious diseases that may be reduced by vaccinations, we require all new appointments to be vaccinated as a condition of employment at our company.
To apply for this job please visit wd1.myworkdaysite.com.